Industrial Tank Lining
Since the 1980's, Ferrous Protection have been widely considered an industry leader in the application of solvent free materials in bulk liquid storage tanks and vessels. Over the years, Ferrous Protection have branched out to offer a range of linings, including epoxy based tank linings, vessel linings, bund linings and GRP linings, vinyl ester based tank linings, vessel linings, bund linings and GRP linings, and polyurea tank linings to name a few.
With over 30 years of experience working both nationally and internationally, including Europe, North America, South America, the Caribbean, India, Asia and the Middle East, for both public and private sector clients including the MOD and Oil Supermajors, Ferrous Protection are excellently positioned to support in almost any in situ corrosion protection requirement.
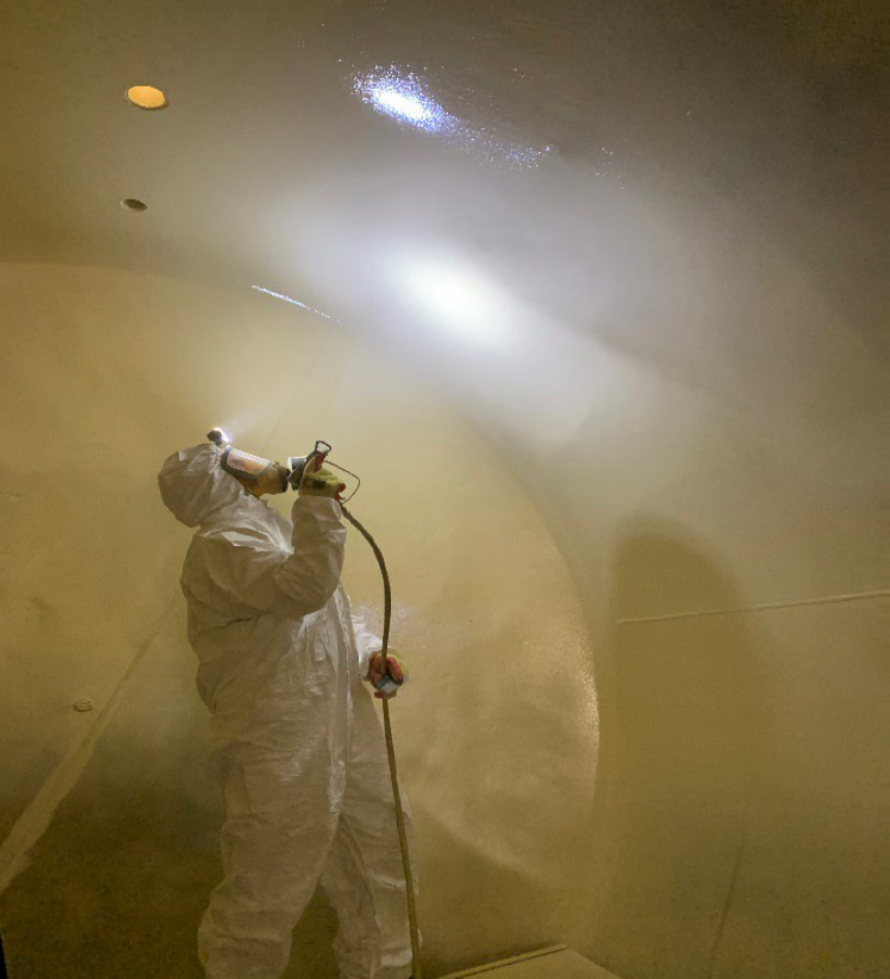
Our tank lining work stretches across various industries including:
- Aviation (Jet fuel tank lining & painting, diesel tank lining & painting, slops tank lining & painting, aviation jet fuel transfer pipeline corrosion protection, pre airfield tank lining & painting, airside tank lining & painting etc.) - See our Aviation Fuel Tank Liner page
- Oil & Gas (crude oil tank lining & painting, external and internal floating roof tank lining & painting)
- MOD (marine diesel tank lining & painting, aviation jet fuel tank lining & painting)
- Chemical processing (sulfuric acid tank lining & painting, nitric acid tank lining & painting, hydrochloric acid tank lining & painting, acid tank lining & painting, caustic tank lining & painting)
- Petrochemical (epoxy and vinyl ester tank lining & painting)
- Manufacturing (bullet tank lining & painting, silo lining & painting, cone down tank lining & painting).
Ferrous Protection have the experience, personnel and knowledge to remove any existing lining, coating, rust or paint system and re-apply a brand new protective lining whether it be for a storage tank, vessel, silo, bund or other steel asset, extending it's life and preventing the need for costly replacement.
Chemical Processing, Petrochemical, Construction, Aviation and Manufacturing.
Examples of tanks in which we regularly install new linings systems:
- Small potable water / effluent / chemical tanks for manufacturing & agricultural use.
- Horizontal bullet tanks used in process manufacturing.
- Semi-buried / underground marine diesel tanks for the MOD.
- 80m+ diameter external floating roof crude oil tanks on major oil terminals & refineries.
- Secondary & primary storage tanks of aviation fuel.
- Storage tanks storing aggressive cargo.
- Rectangular diesel tanks.
- Bulk storage powder silos.
What is Tank Lining?
A tank lining is a protective coating applied to the internal surfaces of a storage tank or vessel. An effective lining may protect the steel from chemical attack or corrosion, protect the stored product from the steel, or even a combination of both. Failure to protect your tank through the application of a suitable lining is likely to:
- Detrimentally impact the quality of your stored product.
- Reduce the life of your tank/vessel.
- Incur significant maintenance / replacement costs which can easily be avoided.
- Increase the risk of loss of containment, posing significant safety and environmental risks and reputational damage.
Why Choose Ferrous Protection to Install Your New Tank Lining?
Ferrous Protection have extensive experience in applying new tank linings into a wide range of tanks and vessels. We offer a variety of support services to allow works to be carried out in situ such as:
- Confined space entry.
- Confined space emergency rescue & standby.
- Powered access.
- Fixed and mobile scaffold access.
- Rope and cradle access.
- Self-permitting.
- Robotic surface preparation & robotic coating application.
- Waste containment and responsible disposal.
Service Offering
Ferrous Protection are capable of utilising a wide range of surface preparation and coating application techniques to ensure the right tools are being used for the job.
Surface Preparation:
- Abrasive blast cleaning (grit blasting, shot blasting, sand blasting)
- Captive blast cleaning
- Vacuum blast cleaning
- Electro-magnetic thermal induction
- Wet / Slurry blast cleaning
- UHP water jetting
- LP/HP water jetting
- Bristle blasting
- Needle gunning
- Grinding / cutting / wire cup brushes
- Mechanical abrasion using aluminium oxide paper
- Vertidrive remote controlled robotic jetting & blasting
Coating Application:
- Single component airless spray
- Plural component airless spray
- Brush
- Roller
- Trowel
- Passive fire protection
- Metal spraying
Ferrous Protection have the experience, personnel and knowledge to remove any existing lining, coating, rust or paint system and re-apply a brand new protective lining whether it be for a storage tank, vessel, silo, bund or other steel asset, extending it's life and preventing the need for costly replacement.
All our works are carried out by suitably trained, competent and experienced personnel who are trained by external providers as well as our in house TrainThePainter certified trainers.
All works are accompanied by a fully detailed, task- and site-specific set of RAMS, emergency rescue plan (where confined space entry is required) and Inspection & Test Plan as well as any other HSQE documentation as required.
Each project is regularly visited by a member of the management team for spot HSQE inspections to ensure the highest levels of safety, professionalism and workmanship are maintained.
The package includes:
- Consultation to establish client exact needs.
- Site survey and inspection as necessary.
- The optimum selection of product and application technique based on previous wide-ranging experience.
- Preparation and submission of a fully detailed and comprehensive project HSQE pack, including task and site specific RAMS, Inspection & Test Plan, MSP Programme Gantt Charts, Emergency rescue plans, operative certs, equipment certs etc.
- The execution of the work to agreed programme, specification and budget constraints by our own experienced operatives and qualified supervision.
- Weekly HSQE site inspections by our qualified and experienced management team.
- Inspection, testing and reporting (total quality management) with a full project QAQC Handover Dossier with warranty paperwork on completion.
- Regular re- inspection at agreed frequency.
Always at the forefront of our thinking is our responsibility to our client, their employees and assets, the environment and our workforce.
We have a range of sustainability initiatives from the use of solvent free and water–borne products, to reducing waste during surface preparation through using environmentally friendly abrasives or captive blasting; and the correct disposal of waste illustrates our commitment to being a responsible and sustainable business by reducing pollution and conserving the environment.
We also believe that cost effectiveness is crucial to our continued success and work closely with our clients to ensure the project is executed in the most effective and efficient way, without cutting corners.
Operating globally, from installing a new GRP epoxy lining to an 77m diameter crude oil tank in extreme heat in Trinidad in 2021, to carrying out critical infrastructure upgrade works to the largest commercial and military air transport hub in the extreme cold in Greenland in 2022, allows us to broaden and enhance our store of knowledge. This we are happy to share with you at your next opportunity.
The Oil and Petrochemical Industry
Our extensive use of solvent free coatings enables us to work with increased safety, better sustainability and greatly reduced risk of fire/explosion. We offer:
- Tank cleaning and waste management.
- Tank linings both on new and existing installations.
- Easy clean coating.
- Refurbishment of floating roofs.
- Refurbishment of tank floors.
- Application of spray and hand lay G.R.P. laminates.
- External coating to tanks, pipelines, structures, pumps and other ancillary equipment.
- Lining secondary containment areas.
- Metal spraying.
- Robotic surface preparation and coating application.
- On time completion of projects.
- We can also offer a full package of the above plus scaffolding, NDT, mechanical repairs, protective coating and lining inspection and insulation inspection as required.
The Chemical Industry
Our extensive knowledge of application procedures, and the suitable resistance of various products available, gives us the opportunity to offer “one call” solutions and pricing, for the protection against most types of chemical storage/contact.
We have successfully completed many projects for the lining/coating of carbon steel, stainless and alloy tanks and vessels, concrete storage pits and bunds also external protection against chemical corrosive atmospheres.
The Food and Brewing Industry
Application of non – taint systems in active production areas is an essential feature in this industry.
Our wealth of experience in this area has resulted in Ferrous Protection having an exceptionally strong reputation in this sector internationally:
- Use of Solvent free and water borne paints and metal sprayed system.
- Use of food grade floor and wall coatings.
- Protection of hot liquor tanks.
- Linings resistant to a wide variety of service temperatures
- Ability to meet programme requirements during “shut down” periods.
The Water Industry
The sector encompasses both “clean” and “dirty” processes. Suitable certified systems are available for potable water. Chemical/ abrasion resistant coatings are used for digestive/effluent/sewage conditions. Ferrous Protection are UVDB certified and can protect all types of substrates through the following:
- WRC approved solvent free and solvented coatings.
- Water – borne approved coatings.
- High quality linings enabling ease of cleaning.
- Long life system complete with performance quarantees.
- Flexible system for concrete substrates.
The Aviation Industry
Ferrous Protection have extensive experience protecting and maintaining both pre-airfield and airside Jet fuel storage tanks and pipework. We are the chosen asset maintenance and surface protection contractor on many of the UK’s largest airports as well as airports overseas including most recently the external coating of 4no tank roofs and pipework at Manchester Airport and the re-lining of 7no Jet A1 fuel storage tanks and corrosion protection of 1.46km of cross country pipeline of Greenland’s largest military and commercial air transport hub.
We can offer:
- Tank cleaning for API653 tank inspections.
- Hazardous waste management.
- Abrasive blast cleaning.
- Application of protective lining systems in accordance with EI-1541.
- Coating and lining inspections.
Repair of a Corroded Tank for a Manufacturing Customer
Client: National Plastics Manufacturing Plant
Location: UK
Contract Value: £18,000
Asset: Adhesive bulk storage conical tank
Project Brief: Ferrous Protection were recently contacted by the Maintenance Manager at a well known plastics manufacturing plant in Manchester. The quality of product stored in one of his chemical tanks was deteriorating and showing signs of internal corrosion of the tank, and the Maintenance Manager was considering disposing of the tank and buying brand new. Ferrous Protection worked with him to inspect the condition of the tank and propose a suitable lining system. Within 2 weeks, he had a fully capable and chemically-resistant lining system installed in his tank which meant:
- minimal disruption to production.
- no logistical hassle of disposing of the old tank and installing the new tank.
- cost savings of 41% in comparison to buying new.
- additional minimum 15 years life of his existing tank.
Request a Call Back
Delivering Tank Lining Solutions Worldwide
Ferrous Protection has successfully completed projects across the UK, Europe, and beyond. With over 30 years of experience, we specialize in providing corrosion protection for tanks in industries such as oil & gas, aviation, and petrochemical. Wherever you are, we can support your tank lining needs.
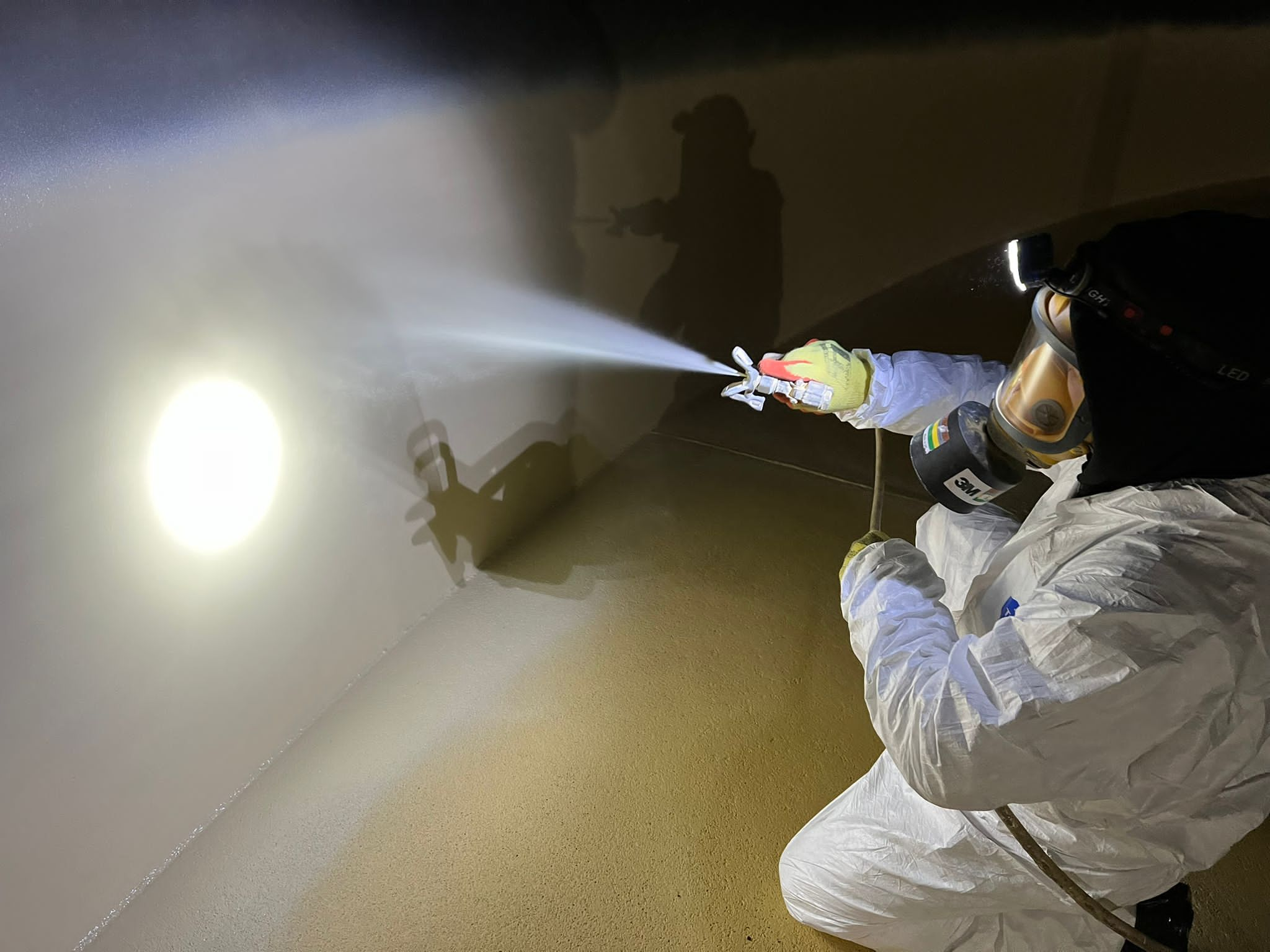
Case Studies
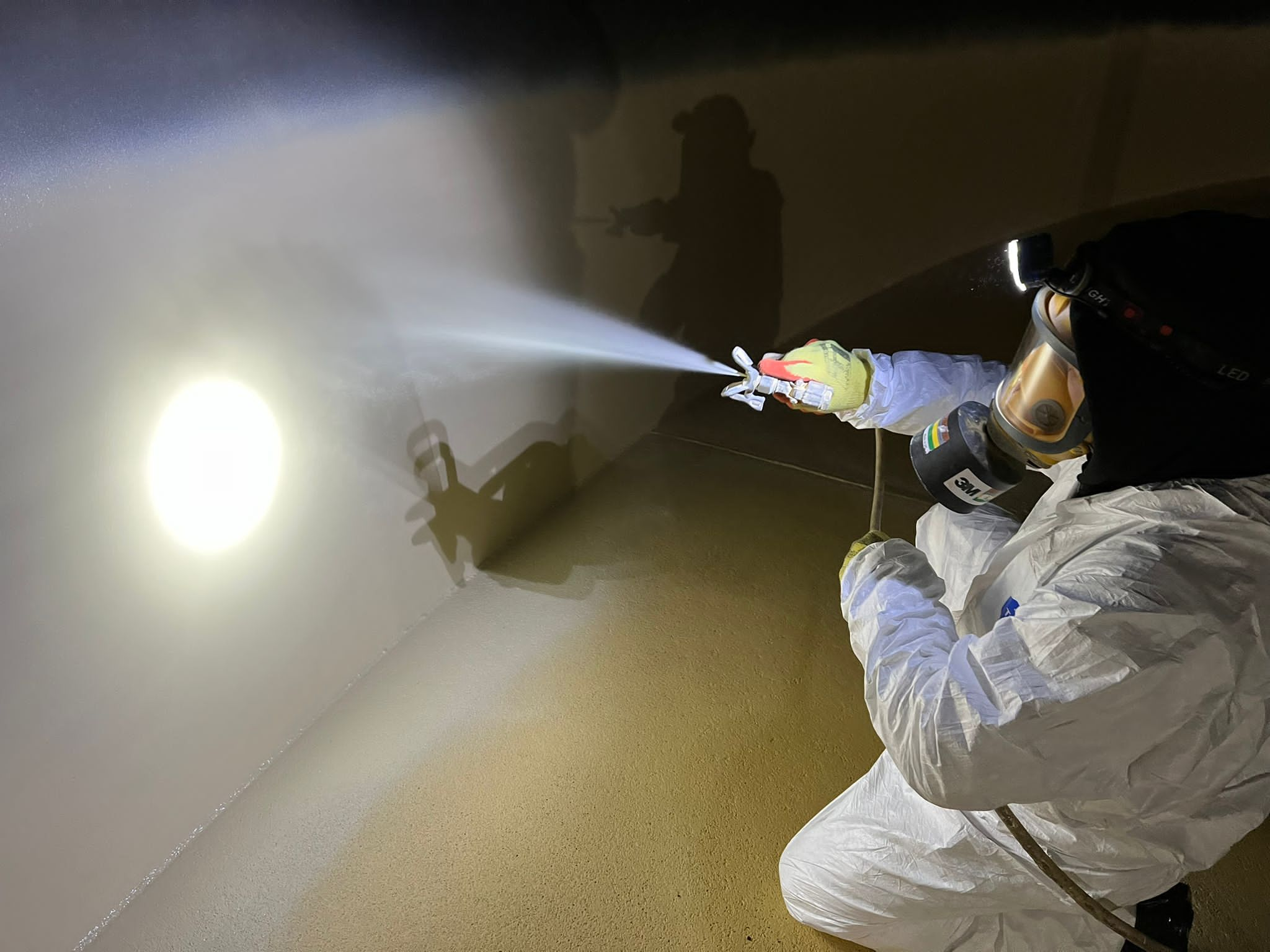
Application of a new lining in an 80m diameter crude oil tank
Client: Leading Global Mid- & Down-Stream Oil Company
Location: UK
Contract Value: £145,000
Asset: 80m diameter external floating roof crude oil storage tank.
Project Brief: Ferrous Protection was recently engaged by a leading global mid- and down- stream oil company in the UK to remove the failed existing lining of an 80m diameter crude oil storage tank and re-apply a two-component, solvent-free, amine-cured novolac phenolic epoxy lining capable of withstanding product temperatures of up to 120°C.
Ferrous Protection carried out a site survey and planned the project to minimise the risk to the personnel and environment so far as was reasonably practicable. We removed the existing lining using a combination of open nozzle grit blasting and captive blasting using 20E automatic blast machines.
Engineering controls were implemented to maintain the specified atmospheric conditions within the tanks and a suitable holding primer was applied by airless spray to the prepared substrates. Once the primer had been applied and "clean conditions" had been implemented within the tank, all welds, edges and intricate areas were stripe coated with the specified lining material and a full lining applied to achieve a uniform film over the entire prepared surface area.
Once the lining had sufficiently cured, a competent and experienced Coatings Inspector carried out a holiday detection test, DFT checks and a thorough visual inspection before signing off the works.
The project was delivered on time and budget and the following comments were given by the Client Appointed Project Engineer:
Client Project Engineer:
"5 stars for Ferrous Protection's overall project management, technical capability and quality of finished work. I found them to be very knowledgeable, helpful and professional throughout, the QA documentation was prompt and very thorough and the the job was done efficiently and to a very high standard with safety and communication being excellent from start to finish."
Installation of a New Protective Lining to a Semi-Buried Storage Tank
Client: Europe’s leading oil & fuel logistics company
Location: UK
Contract Value: £200,000
Asset: 44m dia semi-buried bulk fuel storage tank.
Project Brief: The customer stores fuels in bulk for sale to customers all over the country. It is of paramount importance that the tanks are well maintained to ensure the quality of the stored product meets specific standards. As part of the customer’s periodic asset maintenance programme they took the tank out of service and engaged with Ferrous Protection to first carry out the pre-inspection blast, and then install the new lining system following inspection and mechanical repair work.
For the pre-inspection blast, Ferrous Protection provided confined space safety standby and emergency rescue cover for all works inside the tank. We removed the existing lining and heavy rust to take the surfaces back to bare steel ready for inspection by a combination of abrasive blast cleaning from mobile scaffold and captive blast cleaning.
On our second visit to install the new lining, we implemented engineering controls including dehumidification, dust extraction and heating to ensure safe and specified atmospheric conditions were maintained. We re-prepared the substrates to the specified standard through a combination of abrasive blast cleaning and captive blast cleaning and held the standard by applying a two component, epoxy primer by airless spray. All edges, welds and intricate areas were stripe coated by brush to ensure sufficient coverage, and all pitted areas were given a scrape coat to ensure the epoxy was worked well into the pits. Finally 2no coats of two-component, solvent free novolac epoxy phenolic was applied to the prepared areas by airless spray. Once cured, our ICorr L3 Protective Coating Inspector performed a visual inspection, D.F.T. checks and holiday detection and signed the works off as compliant with the relevant specification and standards.
The project was delivered successfully with no safety or environmental incidents. The contract was brought in on budget and nearly a week ahead of programme. The lining was applied in 100% accordance with the client’s specification and the customer subsequently placed orders with Ferrous Protection for the lining of 4 more thanks within the following 12 months.
Client Projects Manager:
"Ferrous Protection undertook grit blasting works in Tank 4 at our fuel terminal at Station Road, South Killingholme, Immingham, DN40 3ED in 2021. They worked in the capacity of Principal Contractor and under an asset transfer permitted themselves. The project included working with high pressure equipment, confined space working, working with hazardous substances and working at height from mobile towers. The project was carried out safely with 0 accidents recorded. The project was completed successfully."
Testimonials
Don't just take our word for how good we are. Have a look at what our customers say...
Our Clients
We are proud to work with some of the most respected companies across industries.
Our Services
Providing high-quality protective coatings and industrial services.