Surface Preparation
Ferrous Protection offer a range of surface preparation services to remove existing bund linings, tank linings, protective coatings, failing paint systems, mill scale and even heavy rust. It is often said that the key to an effective tank lining, bund lining or protective coating is proper surface preparation. This is why Ferrous Protection offer a vast array of surface preparation methods to ensure the correct standard of cleanliness, surface profile and substrate finish is achieved. Such methods include shot blasting, grit blasting, sand blasting, abrasive blast cleaning, low pressure washing, high pressure washing, ultra high pressure washing, heat induction and mechanical preparation just to name a few. The benefit of using methods such as shot blasting, grit blasting, sand blasting and abrasive blast cleaning include the ability to completely remove even the toughest and most tightly adhering tank linings, protective coatings, bund linings or industrial paints and prepare the surface back to the cleanest standard of bare steel ready for application of the new tank lining, bund lining, industrial paint system or protective coating. Once grit blasting, shot blasting, sand blasting or abrasive blast cleaning has been completing, we will inspect the surface to ensure the correct standard of surface cleanliness is achieved and all the rust, paint, linings, coatings, mill scale and surface contamination has been removed before overcoating with the new tank lining, bund lining, protective coating or intumescent coating system.
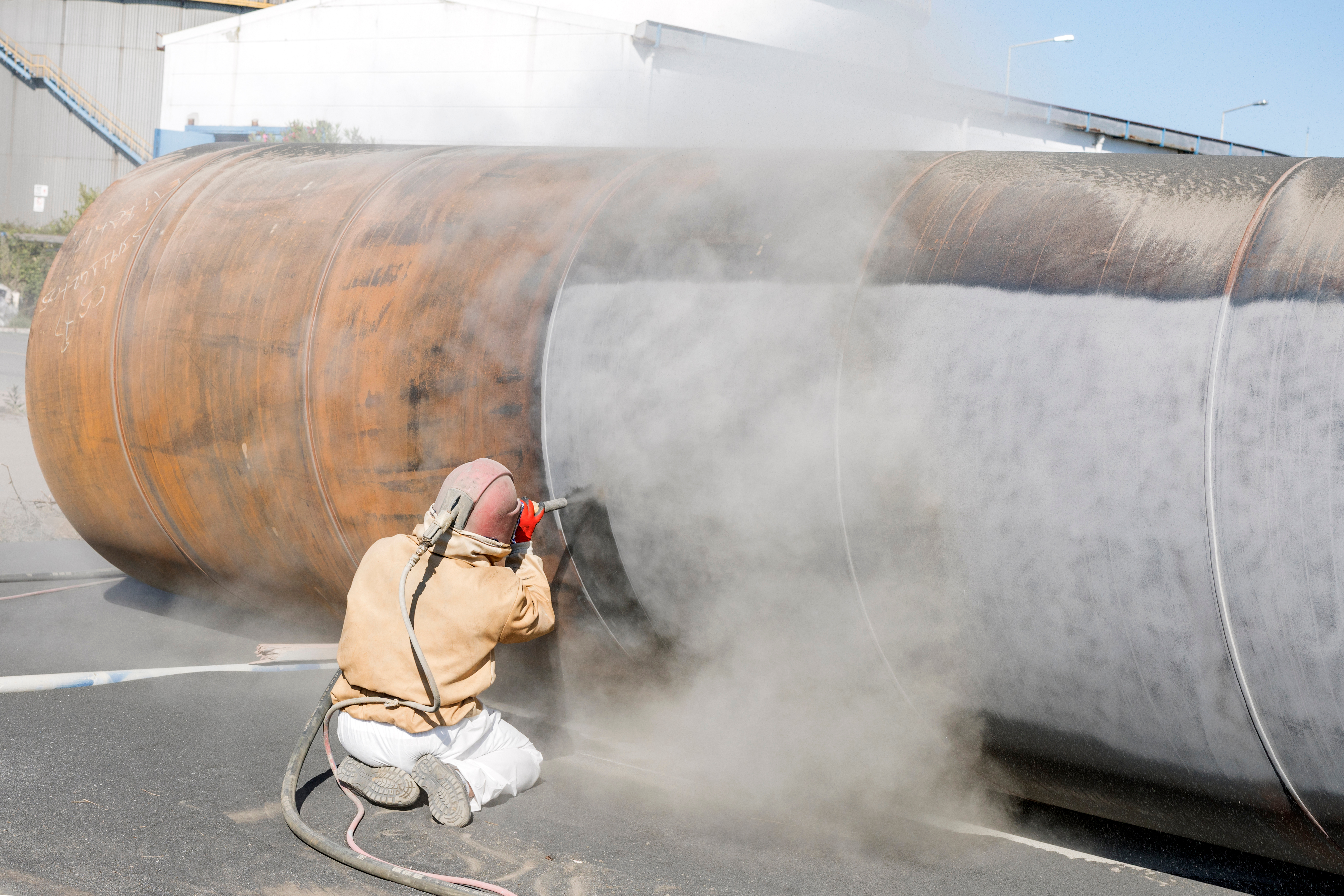
Methods of surface preparation include:
- Grit blasting / Shot Blasting / Sand Blasting - abrasive blast media is forcibly propelled using a nozzle at a metal surface to remove rust, paint, mill scale, existing tank linings, bund linings, protective coatings etc. and prepare the substrate to a clean bare steel finish.
- Captive blasting - a mix of angular and ball blast media is forcibly propelled against a metal surface to remove rust, paint, mill scale, existing tank linings, floor linings, bund linings and protective coatings and prepare the substrate to a clean bare steel finish. The captive blasting machine allows for local recovery and recycling of the blast media, reducing cost, environmental impact and dust.
- Bristle blasting - using a type of handheld tool to mimic the effects of grit blasting, shot blasting, sand blasting and abrasive blast cleaning at much less cost, safety risk and environmental impact. Suitable for small areas.
- Needle gun - a type of handheld tool which forces very fine chisels known as needles against a surface at variable speeds up to 5,000 times per minute to remove small areas of existing coatings, tank linings, industrial paint systems.
- Wet/slurry blasting - similar to grit blasting, shot blasting, sand blasting and abrasive blast cleaning but water is added to the blast media to reduce dust.
- Low / High / Ultra-High pressure water jetting - a very effective means of removing surface contaminants, depending on the operating pressure the water jet can be used to clean the surface prior to grit blasting, shot blasting, sand blasting or abrasive blast cleaning, or it can be used to remove the existing tank lining or protective coating at higher pressures.
- Electro-magnetic thermal induction - specialist kit which uses electro-magnetic thermal technology to reduce the adhesion of an existing tank lining or protective coating which is to be removed.
- Vertidrive crawler systems for remote controlled robotic jetting and blasting - Where access is an issue, the vertidrive crawler system can be used to remotely ascend or desend vertical surfaces or even operate upside down on a horizontal surface to prepare the substrate. Various nozzles can be fitted to the machine to allow it to shot blast, grit blast, sand blast, abrasive blast clean, low pressure wash, high pressure wash and even ultra high pressure wash. A recovery hood can be fitted to the nozzle which allows the blast media or water to be recovered and recycled.
Health & Safety
Our blasting and water jetting operatives are specially trained in the various methods of surface preparation such as grit blasting, sand blasting, shot blasting, pressure washing, mechanical preparation etc. and can achieve a range of standards as required. We operate under an externally audited ISO45001 H&S Management system and maintain an industry leading H&S record to ensure all surface preparation works are carried out to the highest OH&S standards.
Site Surveys
Ferrous Protection have over 35 years of experience in the surface preparation industry, serving customers globally from small private companies to large multi-nationals and public sector bodies. We have an experienced and qualified management team that can carry out site surveys and recommend appropriate surface preparation levels and techniques to meet the customer's requirements.
Request a Call BackLeading Experts in Surface Preparation for Corrosion Protection
At Ferrous Protection, we specialise in advanced surface preparation techniques that form the foundation of all our protective coating and tank lining solutions. With over 30 years of experience, we use cutting-edge technology to ensure the highest levels of cleanliness and surface profile, ensuring optimal adhesion and long-term durability of the protective coatings we apply. From abrasive blasting to robotic surface preparation, we are committed to providing high-quality, efficient, and environmentally responsible surface preparation services for industrial, aviation, and oil & gas projects worldwide.
Case Studies
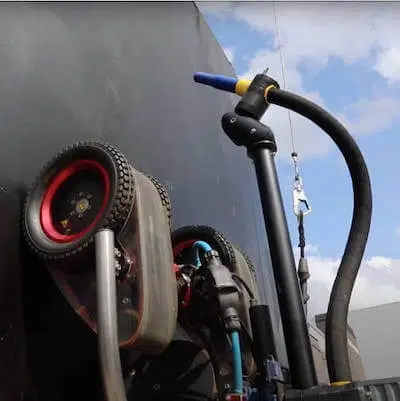
Vertidrive
Ferrous Protection are set up to tackle all elements of site based surface preparation. From erecting encapsulated scaffold through to operating powered access, we can reach almost anywhere... And for the areas we can't reach, we have the Vertidrive - a world leading remote controlled magnetic crawler system with shot blasting and pressure washing capabilities.
Health & Safety Benefits
The Vertidrive can prepare surfaces by grit blasting, shot blasting and Pressure Washing and is a favourite amongst our customers because it reduces the hazard of personnel operating high pressure equipment at height. It has the capability to operate on vertical surfaces and even upside down through the use of magnets and cables, and is operated by a trained and competent operative at floor level using a remote control directing the crawler where to go.
Environmental Benefits
The nozzles can be fitted with vacuum suction units which recover the spent grit or run off water. This is particularly useful when you want to recycle the abrasive or remove lead-based paint. The Vertidrive is an excellent option for environmentally-sensitive works.
Demo
To book in for a demo, don't hesitate in contacting us!
Surface preparation is the essential treatment of the substrate or surface that is required to allow other works to be carried out. Certain standards of cleanliness or preparation are required depending on what it is being prepared for, for example NDT inspection, mechanical repairs, lining or coating application etc. The purpose of the surface preparation works usually dictates the standard of cleanliness required, which in turn determines the method of surface preparation.
Over 90% of premature protective coating or tank lining failures are a result of improper or inadequate surface preparation. Ensuring proper surface preparation to the correct standards of cleanliness is critical to ensuring the longevity and intended performance of any protective coating or tank lining. Before applying any protective coating or tank lining, the surface or substrate must be suitably cleaned to remove any grease, dirt, grime, algae/growths, soluble salts, failed existing coatings, rust etc. down to within acceptable parameters. Having a competent surface preparation contractor such as Ferrous Protection Ltd who understands these parameters and how to properly test for them is paramount to achieving a successful surface preparation and protective coating project.
There is a wide range of surface preparation techniques on the market, each with its advantages and disadvantages. Having a competent surface preparation partner such as Ferrous Protection is critical in ensuring the most appropriate surface preparation technique is chosen to ensure the project is delivered safely, sustainably and to the required standards.
. Such methods of surface preparation include:
- Abrasive Blast-Cleaning (Shot Blasting, Grit Blasting): Using pressurised air to propel abrasive material against a substrate to remove contaminants and create a textured surface.
- Wet Abrasive Blast-Cleaning (Wet Blasting): Using pressurised air to propel abrasive material against a substrate to remove contaminants and create a textured surface, including a water stream at the nozzle to suppress dust.
- Power Tool Cleaning: Using rotary wire brushes, bristle blasters, grinding disks etc. to clean the localised areas of corrosion or coating failure.
- Water Jetting: Utilising a range of low, high and ultra-high pressure water jets to achieve varying levels of surface cleanliness from removal of contaminants through to complete removal of an existing coating back to bare steel.
- Chemical Cleaning: Applying specialised chemicals to dissolve or remove contaminants like oil and grease.
- Robotic Crawlers: Magnetic remotely controlled units with vacuum recovery heads that can grit blast and water jet surfaces without the need for personnel to work at heights.
- Electro-magnetic Thermal Induction: This specialised approach reduces the adhesion of existing coatings for easier removal.
Ferrous Protection recently abrasive blast-cleaned from fixed scaffold the internal of a bulk liquid storage tank at a major UK airport. To avoid introducing trace copper into the tank which can present safety hazardous in Jet-A1 tanks, garnet (an inert, naturally occurring semi-expendable mineral abrasive) was used. The experienced and competent grit blasting operatives blasted off the existing lining from the floor, shell, roof and roof structure to ISO8501-1 Sa2½ standard of cleanliness and the garnet impacted the steel at high speed to create an angular surface profile of 50-75 microns. This provided the tank internal with optimum surface preparation conditions for re-application of a highly effective chemical and corrosion resistant tank lining. This level of surface preparation gives the tank lining the best possible chance of protecting both the asset and jet fuel for many years to come and provide the asset owner with complete peace of mind.
The most suitable method of industrial surface preparation is typically decided by the level of surface cleanliness required. This is usually determined by the type of coating to be applied and the nature of the site/asset to be treated. For example, there are various surface tolerant coatings available on the market that are designed to offer optimal adhesion over lower standards of cleanliness such as substrates prepared by water jetting or power-tool cleaning. Other coatings such as metal spray, zinc based coatings require higher levels of surface preparation such as ISO8501-1 Sa3 which can only be achieved by abrasive blast-cleaning.
The site and asset can also affect the type of surface preparation used on a project, for example if the existing coating is lead based or over a water course, abrasive blast-cleaning is often considered not the most suitable means of surface preparation due to the risk of environmental pollution, in which case using systems with vacuum recovery hoods or mechanical cleaning may be considered.
If the existing coating is largely intact and sound with only localised areas of corrosion or mechanical breakdown, they asset owner may decide to perform localised “touch ups” rather than fully removing and re-coating, in which case low pressure water jetting and mechanical cleaning can be utilised to remove contaminants and bring any corroded areas back to bare steel reading for patch coating repairs.
Surface preparation typically involves the use of electric or pneumatic equipment operating at high voltage or pressures. They can also involve hazardous materials and processes and require to be carried out in high risk areas such as at height or in confined spaces. Ensuring surface preparation works are performed safely and to the relevant health and safety standards is critical in achieving project success. Ferrous Protection prioritises safety by:
- Utilising advanced technology and techniques to carry out surface preparation works.
- Using only highly competent, trained and experienced surface preparation prfoessionals to perform works.
- Undertake high level surface preparation training at our premises by qualified and time served trainers.
- Lead abatement provisions in line with CLAW regulations for removing lead based coatings such as medical surveillance (lead in blood tests), lead in air monitoring, decontamination facilities etc.
- Having robust safety procedures and systems including robust sets of task- and site-specific RAMS for each project.
- Utilising appropriate personal protective equipment (PPE) and respiratory protective equipment (RPE) for workers.
- Where required, implementing forced ventilation and forced extraction through utilising engineering controls to maintain high levels of visibility.
Oftentimes, surface preparation requires the use of hazardous materials and also the removal of hazardous materials. These can include oil contaminated washings from pressure washing, to lead dust from blasting lead contaminated paint. Each project will present its own environmental hazards which will be thoroughly risk assessed by Ferrous Protection Ltd’s HS&E team to ensure suitable and sufficient control measures are in place. We work with a properly vetted and reputable supply chain for our waste management services and can carry out various waste characterisation tests to ensure the correct disposal routes and waste streams are used. Where possible, all environmental and pollution hazards will be minimised by taking the sustainable alternative, for example using inert and naturally occurring abrasives or captive blasting over expendable abrasives. Scaffold and shrink wrap encapsulated habitats can also be utilised to create our own work area to ensure no hazardous materials escape to the local atmosphere. Other projects allow for vacuum recovery systems which remove the spent grit / washings immediately from the workface.
Yes. Ferrous Protection employ several ICorr Protective Coating Inspectors who are specially trained in all methods of surface preparation and protective coating techniques. If you are not sure on the most appropriate surface preparation technique for your project, don’t hesitate to get in touch for some advice or to arrange a site survey to discuss your requirement in more detail.
Testimonials
Don't just take our word for how good we are. Have a look at what our customers say...
Our Clients
We are proud to work with some of the most respected companies across industries.
Our Services
Providing high-quality protective coatings and industrial services.